Tractor-Mounted Auger Easy To Move
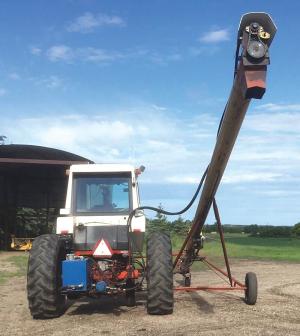 ✖  |
Ice and snow can make it tough to position large augers, but not for Mickey Heneghan. His tractor-mounted, 41-ft., 10-in. auger is easy to place and to move from one bin to another. Best of all, it didn’t require major modifications on either unit, and it can be removed with 2 bolts.
“We farm in western Manitoba, and winter weather can make positioning large augers a challenge,” says Heneghan. “That’s before you try to cold-start the small engine to power the auger.”
Heneghan positioned the auger so one wheel is under the tractor and then ran a push/pull brace between the tractor drawbar and the auger axle. In order to position the auger wheel under the tractor, he extended that end of the auger’s axle by about 17 in. A second brace runs perpendicular from the front of the tractor to the frame of the auger. It acts as a steady bar to keep the auger in line with the tractor.
The 1 by 3-in. push/pull brace (fabricated from 2 pieces of angle iron) is about 20 in. long. It is pinned to a clevis type bracket on a 3-in., angle iron crossarm that bolts to the drawbar mount. The clevis pin allows the auger axle to flex over uneven ground separate from the tractor.
The push/pull brace is welded to a 12-in. length of pipe that Heneghan slipped over the end of the extended axle. A 3/4 by 3/4-in. piece of steel welded to the extended axle keeps the pipe sleeve in place.
The steady bar is an 84-in. long, 2-in. diameter steel pipe. It is bolted to the front of the tractor frame and pinned to a clevis bracket at the auger. The clevis is bolted to the mounting plate on the auger for the auger frame.
Heneghan welded a second mounting plate to the auger pipe just ahead of the steady bar. A caster wheel is welded to a steel strut that is pinned to the mounting plate. A hydraulic cylinder attached at the bottom of the strut makes it easy to raise or lower the intake end of the auger for transit or use.
The caster wheel hydraulic cylinder is pinned to a reinforcing, 25-in. long, cross brace on the auger frame.
Most of the materials that went into the project were salvaged. One challenge Heneghan couldn’t fabricate for was hydraulic power. His tractor had 16 gpm flow, but he needed 25 gpm. Another out-of-pocket expense was a 1,000-rpm orbital motor mounted at the top of the auger to power the flighting.
“The entire project ran about $2,200 with most of that being the pto-powered pump and the hydraulic motor,” says Heneghan. “I had previously replaced the manual crank with an orbital motor to raise and lower the auger. Everything can be done from the tractor seat.”
Contact: FARM SHOW Followup, Michael Heneghan Box 389, Rossburn, Man. R0J 1V0 Canada (ph 204 859-2241; heneghan527@gmail.com).
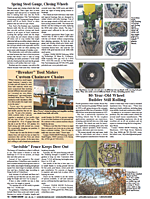
Click here to download page story appeared in.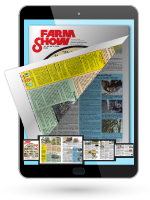
Click here to read entire issue
Tractor-Mounted Auger Easy To Move Ice and snow can make it tough to position large augers but not for Mickey Heneghan His tractor-mounted 41-ft 10-in auger is easy to place and to move from one bin to another Best of all it didn’t require major modifications on either unit and it can be removed with 2 bolts “We farm in western Manitoba and winter weather can make positioning large augers a challenge ” says Heneghan “That’s before you try to cold-start the small engine to power the auger ” Heneghan positioned the auger so one wheel is under the tractor and then ran a push/pull brace between the tractor drawbar and the auger axle In order to position the auger wheel under the tractor he extended that end of the auger’s axle by about 17 in A second brace runs perpendicular from the front of the tractor to the frame of the auger It acts as a steady bar to keep the auger in line with the tractor The 1 by 3-in push/pull brace fabricated from 2 pieces of angle iron is about 20 in long It is pinned to a clevis type bracket on a 3-in angle iron crossarm that bolts to the drawbar mount The clevis pin allows the auger axle to flex over uneven ground separate from the tractor The push/pull brace is welded to a 12-in length of pipe that Heneghan slipped over the end of the extended axle A 3/4 by 3/4-in piece of steel welded to the extended axle keeps the pipe sleeve in place The steady bar is an 84-in long 2-in diameter steel pipe It is bolted to the front of the tractor frame and pinned to a clevis bracket at the auger The clevis is bolted to the mounting plate on the auger for the auger frame Heneghan welded a second mounting plate to the auger pipe just ahead of the steady bar A caster wheel is welded to a steel strut that is pinned to the mounting plate A hydraulic cylinder attached at the bottom of the strut makes it easy to raise or lower the intake end of the auger for transit or use The caster wheel hydraulic cylinder is pinned to a reinforcing 25-in long cross brace on the auger frame Most of the materials that went into the project were salvaged One challenge Heneghan couldn’t fabricate for was hydraulic power His tractor had 16 gpm flow but he needed 25 gpm Another out-of-pocket expense was a 1 000-rpm orbital motor mounted at the top of the auger to power the flighting “The entire project ran about $2 200 with most of that being the pto-powered pump and the hydraulic motor ” says Heneghan “I had previously replaced the manual crank with an orbital motor to raise and lower the auger Everything can be done from the tractor seat ” Contact: FARM SHOW Followup Michael Heneghan Box 389 Rossburn Man R0J 1V0 Canada ph 204 859-2241; heneghan527@gmail com