2020 - Volume #44, Issue #5, Page #18
[ Sample Stories From This Issue | List of All Stories In This Issue | Print this story
| Read this issue]
Splitter Side-Mounted On Old Allis
![]() |
“My dad started heating his house and shop in his 40’s with wood he split by hand,” says Steve. “When he was in his early 80’s, he decided it was time to get a splitter. We decided to take the old C and give it a dignified use. We finished in 2009. At 93, my dad still uses it along with an 80-year-old logging trailer.”
Worth’s father bought the C in 1950 with a hillside plow, cultivator and a disc, all for $1,700. The C was designed to be fitted with an undercarriage mower. The Harmans used 11 gauge, 2 by 2-in. steel tubing to fabricate a support frame for the splitter, the Barnes 2-stage pump, a 10-gal. reservoir and a tool pan. They modeled the frame after the mower frame with the splitter to the right side of the tractor. The 12-gauge steel, 10 by 10 by 24-in. reservoir sits between the splitter and the tractor. A 48-in. long, 13 1/2-in. wide by 10-in. deep tool pan for axes, chainsaw and other tools is centered under the support frame. At the rear, the framework replaces the OEM drawbar yoke assembly to mount the pump and hitch.
“We put the splitter as close to the tractor as we could without worrying about a split log hitting the engine,” says Harman. “When we flip it vertical, the base rests on the ground.”
The splitter is a SpeeCo SplitMaster. It pivots on a piece of 2 by 2-in. steel tubing attached to the support frame.
The Harmans took advantage of the C’s belt pulley shaft that emerges at a 90-degree angle to the rear pto shaft. Initially they used a belt drive from the shaft to the hydraulic pump. Excessive slippage led them to replace it with a chain drive, which in turn was replaced with a toothed belt drive.
“The chain drive worked, but it was noisy and created a lot of vibration,” says Harman. “The toothed belt drive has worked fine. We fabricated a shield over it to keep out little fingers.”
A 6 1/2-in. drive pulley on the belt pulley shaft-drives a 2 3/4-in. pulley on the pump shaft. The pump is mounted to a sliding angle-plate assembly with the shaft secured in single-row ball bearings retained by snap rings.
The plate assembly is bolted to a slotted bottom plate welded between the rear ends of the support frame square tubes. Belt tension is adjusted using 2 horizontal 3/8-in. bolts threaded through the assembly and against the bottom plate.
The restoration included a new paint job. While the C originally had the darker AC (Persian #1) orange, Worth preferred the brighter (Persian #2) orange introduced in 1960. The splitter was painted AC cream with an AGCO sticker for an OEM look.
Contact: FARM SHOW Followup, Steve Harman, 1190 E. Choctaw Dr., London, Ohio 43140 (ph 614 529-4130; steve@tubulartechniques.com).
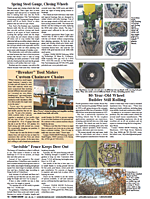
Click here to download page story appeared in.
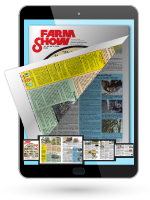
Click here to read entire issue