2019 - Volume #43, Issue #1, Page #15
[ Sample Stories From This Issue | List of All Stories In This Issue | Print this story
| Read this issue]
“Made It Myself” Best Buy Tractor
![]() |
![]() |
“I built it using components from an old Toyota,” says Christensen. “I fabricated a frame with 2-in. sq. steel tubing and laddered it with 1-in. tubing.”
He made the frame narrow to make working in the woods easier. That made it necessary to narrow the Toyota rear end to fit and to respline the axles to match up.
He mounted the 1600cc motor, 4-speed transmission, clutch plate cylinder, radiator, foot pedals and more on the new frame. However, to slow down the drive speed, he needed to do significant gear reduction.
“I mounted a jackshaft with large and small sprockets on pillow block bearings alongside the driveshaft,” explains Christensen. “I cut the splined end off and welded a small sprocket on the driveshaft. I ran a roller chain from it to a large sprocket on the driveshaft stub coming out of the rear end.”
The combination of small to large did what he had hoped. In first gear, the tractor moves slower than a walk. The driveshaft from the transmission extends through the first small sprocket to a freewheeling bearing on the large driveshaft mounted to the rear end. If either roller chain is disconnected, the rear end is completely freewheeling.
At the front end, Christensen fabricated a steering axle using bored out strut castings from the Toyota and king pins from a Ford. He machined new spindles. A pivot in the center lets the front end articulate side to side like a regular straight axle.
“I used the Toyota steering wheel and system under the dash,” says Christensen. “I put a U-joint on the steering wheel shaft so the wheel can be tilted up for easier access.”
Keeping the tractor simple, Christensen skipped any rear suspension, relying on monster mud tires to cushion the ride. In order to mount them, he had to drill out the centers of their wheels to match the Toyota hub. He also fabricated his own fuel tank, body metal and rims.
Headlights came from an auto parts store, as did after market oil pressure, amp and temperature gauges.
There were some temporary modifications made when he used it to drill his well.
“I wanted to drill a sandpoint well in my pasture,” recalls Christensen. “My brother got a boom truck from work, and we set up an old 75-ft. tall windmill tower and hung a pulley in the top. I drilled the first bit and then put a weight on the sandpoint and ran a rope from it through the pulley to my tractor.”
To get the repetitive motion necessary to drive the sandpoint, Christensen anchored his tractor and raised the rear end just off the ground. He dug a hole next to the wheel and fastened a plank to extend about 3 ft. beyond the wheel.
“We attached the rope to the plank and started the wheel moving,” recalls Christensen. “Every time the plank went around, it raised the weighted sandpoint and dropped it back down into the hole. Every time we drove it 8 ft., we would add a coupling and a length of pipe and repeat the process.”
Before long, the two had driven the sandpoint 30 ft. into the ground. With the help of an old Red Jacket pump Christensen rebuilt, water flowed into a stock tank with overrun into a pond.
Contact: FARM SHOW Followup, David Christensen, 6652 Eagle Lake Dr., Maple Grove, Minn. 55369 (ph 763 537-8487; djc2@usfamily.net).
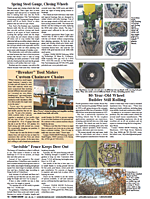
Click here to download page story appeared in.
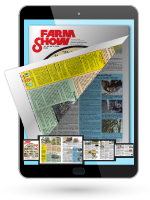
Click here to read entire issue