Shop-Built Liquid Applicator Handles Two Products At Once
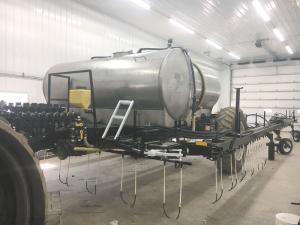 ✖  |
“Saving one or two trips across all our corn acres by side dressing and applying herbicide in one pass will probably pay for what we’ve got into this machine within 2 years,” says southern Minnesota farmer Andy Mulvihill, who worked with his brother, Tony, and father, Tim, to come up with the idea.
The new applicator replaces a self-propelled sprayer that was also used to side-dress urea when a dry tank was installed. They also hired additional custom spraying for burn-down applications.
“Now that we’ve got one machine with a 30-ft. wider boom, we can get our applications done exactly when they’re needed, we don’t have to switch out the RoGator, and we don’t have the extra expense of custom spraying,” Andy says.
They built the applicator by combining the framework and parts from two used sprayers, one with a 90-ft. boom and another with a 60-ft. Fifteen feet were added onto each end of the 90-ft. boom to create the new 120-footer. The boom frame has a 5 by 5-in. back beam and a 3 by 5-in. front beam. It’s hinged at 65 ft. and supported by swivel caster wheels.
Andy says he used schematics supplied by Fast, the company that built the original sprayers, to build the new boom. He wanted two 60-ft. sections, but the existing framework required one at 65 ft. and the other at 55 ft. Breakaways at each end are 6 ft. long.
To make a new cart frame, Andy cut the front platform and hitch off the 90-ft. cart and added new steel to build a reinforced frame 6 ft. longer. Wheel mountings were positioned 5 ft. further back than on the original cart, so the 1,600-gal. tank in the back could be centered over the 18.4 x 38-in. tires. Andy says that helps offset the hitch weight created by the 1,000-gal. herbicide tank mounted crossways on the front.
Liquid is pulled from each tank with two Ace hydraulic pumps and directed into separate manifolds mounted in front of the herbicide tank. One manifold is configured to apply liquid N, and the other handles herbicide. Both tanks have agitation pumps. In-line valves allow both products to run simultaneously, or one can be turned off, and the other will still run. Andy controls application rates with an InCommand 1200 Ag Leader monitor on the tractor.
Two sets of supply lines run the full length of the booms. The back one is used for herbicide, and drop nozzles on the front set apply the liquid N. The monitor allows him to variable rate the N according to field maps loaded in the computer. The applicator’s tanks can be filled at the same time with 3-in. supply lines that feed from their semi-trailer-mounted tender.
“The toughest part of building this was doing the boom layout beforehand, making sure it would fold properly without pinching hoses or bending metal,” Andy says. “I had a few glitches along the way, like breakaways that didn’t work quite right, but nothing major that I couldn’t re-work.”
Andy figures they spent about 400 hrs. building the applicator and about $20,000 on the second used sprayer, tanks, steel, and other parts they needed. They were able to sell some unused duplicate parts to offset part of the expense. “Now we can do two jobs at once with a larger machine, save trips across the field and be done in less time than before,” he says.
The big applicator is one of several projects the Mulvihills have built or renovated since the boys began working on complicated layouts and complex welding projects while in high school in the early 2000’s. “We’re not afraid to tackle big projects because we talk things over and do a lot of planning and layouts before moving ahead,” says Andy. The brothers and their dad all have full-time jobs off the farm and together with their mother Susan, who handles the farm accounting and hauls most of the grain, they still efficiently run about 1,400 acres of corn and beans, most of it irrigated.
“All of us are extremely busy, so when it’s time to plant, spray, irrigate, or harvest, we have to be ready to roll,” says Andy.
Contact: FARM SHOW Followup, M&S Family Farms, 25789 Northfield Blvd., Hampton, Minn. 55031 (andy.mulvihill@yahoo.com).
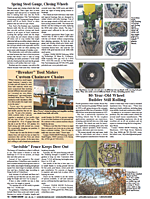
Click here to download page story appeared in.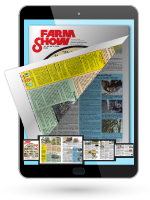
Click here to read entire issue
Shop-Built Liquid Applicator Handles Two Products At Once SPRAYING Miscellaneous “Saving one or two trips across all our corn acres by side dressing and applying herbicide in one pass will probably pay for what we’ve got into this machine within 2 years ” says southern Minnesota farmer Andy Mulvihill who worked with his brother Tony and father Tim to come up with the idea The new applicator replaces a self-propelled sprayer that was also used to side-dress urea when a dry tank was installed They also hired additional custom spraying for burn-down applications “Now that we’ve got one machine with a 30-ft wider boom we can get our applications done exactly when they’re needed we don’t have to switch out the RoGator and we don’t have the extra expense of custom spraying ” Andy says They built the applicator by combining the framework and parts from two used sprayers one with a 90-ft boom and another with a 60-ft Fifteen feet were added onto each end of the 90-ft boom to create the new 120-footer The boom frame has a 5 by 5-in back beam and a 3 by 5-in front beam It’s hinged at 65 ft and supported by swivel caster wheels Andy says he used schematics supplied by Fast the company that built the original sprayers to build the new boom He wanted two 60-ft sections but the existing framework required one at 65 ft and the other at 55 ft Breakaways at each end are 6 ft long To make a new cart frame Andy cut the front platform and hitch off the 90-ft cart and added new steel to build a reinforced frame 6 ft longer Wheel mountings were positioned 5 ft further back than on the original cart so the 1 600-gal tank in the back could be centered over the 18 4 x 38-in tires Andy says that helps offset the hitch weight created by the 1 000-gal herbicide tank mounted crossways on the front Liquid is pulled from each tank with two Ace hydraulic pumps and directed into separate manifolds mounted in front of the herbicide tank One manifold is configured to apply liquid N and the other handles herbicide Both tanks have agitation pumps In-line valves allow both products to run simultaneously or one can be turned off and the other will still run Andy controls application rates with an InCommand 1200 Ag Leader monitor on the tractor Two sets of supply lines run the full length of the booms The back one is used for herbicide and drop nozzles on the front set apply the liquid N The monitor allows him to variable rate the N according to field maps loaded in the computer The applicator’s tanks can be filled at the same time with 3-in supply lines that feed from their semi-trailer-mounted tender “The toughest part of building this was doing the boom layout beforehand making sure it would fold properly without pinching hoses or bending metal ” Andy says “I had a few glitches along the way like breakaways that didn’t work quite right but nothing major that I couldn’t re-work ” Andy figures they spent about 400 hrs building the applicator and about $20 000 on the second used sprayer tanks steel and other parts they needed They were able to sell some unused duplicate parts to offset part of the expense “Now we can do two jobs at once with a larger machine save trips across the field and be done in less time than before ” he says The big applicator is one of several projects the Mulvihills have built or renovated since the boys began working on complicated layouts and complex welding projects while in high school in the early 2000’s “We’re not afraid to tackle big projects because we talk things over and do a lot of planning and layouts before moving ahead ” says Andy The brothers and their dad all have full-time jobs off the farm and together with their mother Susan who handles the farm accounting and hauls most of the grain they still efficiently run about 1 400 acres of corn and beans most of it irrigated “All of us are extremely busy so when it’s time to plant spray irrigate or harvest we have to be ready to roll ” says Andy Contact: FARM SHOW Followup M&S Family Farms 25789 Northfield Blvd Hampton Minn 55031 andy mulvihill@yahoo com