2016 - Volume #40, Issue #4, Page #28
[ Sample Stories From This Issue | List of All Stories In This Issue | Print this story
| Read this issue]
Old Cat Dozer Gets New Life
![]() |
![]() |
“I took about three wheelbarrows full of mud out of it,” says Rodler. “Steering clutches were down to ribbons, control levers were worn out, the battery box was mostly corroded away, and the blade was down to less than 1/8 of an inch. However, all I had to do to the 318 diesel engine was change oil!”
The list of what Rodler had to replace or rebuild was almost as long as the original component list for the big Cat. He did it, in part, because of the basic quality of older equipment.
“This old equipment is made from quality material,” says Rodler. “Every part was high quality, not just the wear parts. They were easy to maintain, too. All you needed was a crescent wrench, screwdrivers, vice grip and a few wrenches, plus a can of ether to start the big engine when cold.”
Rodler points to the quality of the hydraulic cylinders, another component that needed no rebuilding. Even though there was a spot on each ram where the chrome was worn off, they didn’t leak.
“The hydraulic pump looked like it had a leak when it started, as it might drip a little, but it was a friction fit,” he explains. “After an hour of running or when used frequently, there was no leak.”
A few of the new parts included the steering bands, track tension adjusters and guards (replacing old threaded rod types with hydraulic adjustors), belts, brake bands, and control arms for the winch, cables, alternator to trickle charge the pony motor (originally there was no charging system), a seat, and armrests.
Some parts were OEM replacements. Others were harder to find, like a magneto that he sourced from a U.S. company.
Many parts were fabricated by Rodler. These were as simple as building up existing material with his welder to building the equipment needed to make the new build or rebuild.
“The push beams and trunnion ball were not quite worn out, but from what I could see, they'd never been replaced,” says Rodler. “I built the cup up and reshaped it to fit the trunnion ball using 10018 electrodes.”
Rodler took the track apart to work on the linkages, making brass bushings to tighten them up. Before he could do that, he had to bust loose the rusted tight bolts.
“I made up a hydraulic press with a channel-type system to cradle the track,” says Rodler. “I put 10-ton pressure on them and heated them with an oxy torch. Then I hit them with a maul to jar them. With the heat, it broke the bolts apart.”
Rodler notes that the pins with grease fittings on the linkages were worn, but he did a little lathe work and then increased the size of the bushings to compensate.
“I could've gotten new linkages, but that high-grade steel can’t be found today,” says Rodler. “I have about $15,000 to $20,000 in the total rebuild, but the tracks alone are worth many times that. We’ll never again see the quality of that old steel.”
Other steel work included rebuilding control levers and replating the stripped-out undercarriage and the blade with 3/8-in. AR250 plate steel. He also built up the carrier rollers.
“I made a special bench vice to hold the rollers with an electric motor that turned them slowly as I rewelded them, building them up about 5/8-in. across the entire surfaces,” explains Rodler. “I used 10018 electrodes to build up all four of them. I had to watch to not overheat them in order to maintain tensile strength.”
While the diesel engine required practically no work, the pony engine used to start it was a mess. The starter was seized up and needed a complete rebuild with new brushes and bushings. The pony required all new cables, a battery, and a shutoff valve for the fuel line.
“The flywheel had to be realigned. Belts were rotten, and I had to rebuild the battery box,” says Rodler.
Rodler fabricated a safety cage and rebuilt the seats and armrests using material from a salvaged airplane gas tank bladder. It happened to be at a scrap yard when he stopped by.
“I start it occasionally to keep it moving,” says Rodler. “One winter when we had a lot of snow, I slipped off the road with my Pettibone loader. I took the dozer out, set it at idle, and let the winch pull the big Pettibone out.”
Contact: FARM SHOW Followup, Walter Rodler, P.O. Box 695, Debert, Nova Scotia, Canada B0M 1G0 (ph 902-641-2114; swrodler@eastlink.ca).
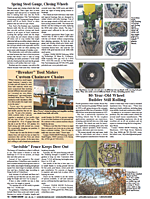
Click here to download page story appeared in.
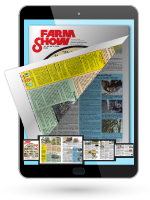
Click here to read entire issue