Manitoba Farmer Built Robotic Steering System
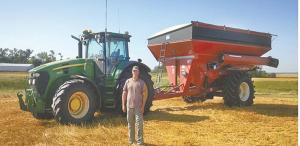 ✖  |
Manitoba farmer Matt Reimer uses an electronically steered tractor to pull his grain cart and in the process figures he’ll save close to $5,000 a year in harvesting costs. Reimer controls the tractor on-the-go from a laptop inside his combine. He assembled the operating system himself using funds he got as a Christmas present in 2014.
Reimer says he doesn’t have any special education in computer programming or electronics, but the assistance provided by 3D Robotics, a company that normally builds autopilot systems for aircraft, proved invaluable. The program he uses has processor and sensor technology from ST Microlectronics and a NuttX real-time operating system. Those items can be harnessed to any autonomous vehicle for about $260.
Since the programming and electronics are open source, Reimer says it was easy to set the system up for his tractor. The guidance system controls actuators that operate controls on his Deere 7930 tractor. The tractor has a CVT gearbox that allows it to operate in the field and stop without changing gears or stalling. The engine operates continuously at 1,500 rpm’s and uses an Outback hydraulic control valve for steering.
When he was putting the system together he learned that it was necessary to use a wheel angle sensor to soften the Pixhawk’s guidance signals so the tractor turns would be more gradual. He took online training to develop programming skills so he could write about 600 lines of code to operate the system. Aside from a small oil leak and a few stops for overheating, the system operated flawlessly during the 2015 harvest.
Reimer says the system has fail safe steps built in to keep the tractor within view whenever they call it to the combine or in the field. The 3D robotics digital radio that controls the tractor and the Pixhawk have a range of just over a mile. The tractor will stop if it’s out of radio range.
Drivers filling their trucks from the grain cart use wireless key fobs to interrupt the signal from the controller so it doesn’t move unexpectedly as they’re unloading. Reimer says he has replaced the labor of one person who’d normally operate the grain cart full time and put it to work in other parts of their farming operation. In the winter of 2015-2016 he hopes to experiment with another system that might let him operate a second driverless seeding unit in the same field where he’s operating his planter. He thinks a self-steering tractor could also be used for harrowing and rolling crops that now require a person to drive the tractor.
Contact: FARM SHOW Followup, Matt Reimer, 4-1-17 N.E., Killarney, Manitoba R0K 1G0 Canada (ph 204 523-8437).
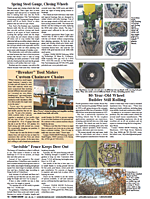
Click here to download page story appeared in.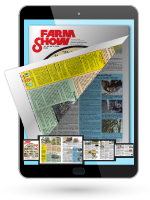
Click here to read entire issue
Manitoba Farmer Built Robotic Steering System SPECIALTY/SERVICES Manitoba farmer Matt Reimer uses an electronically steered tractor to pull his grain cart and in the process figures he’ll save close to $5 000 a year in harvesting costs Reimer controls the tractor on-the-go from a laptop inside his combine He assembled the operating system himself using funds he got as a Christmas present in 2014 Reimer says he doesn’t have any special education in computer programming or electronics but the assistance provided by 3D Robotics a company that normally builds autopilot systems for aircraft proved invaluable The program he uses has processor and sensor technology from ST Microlectronics and a NuttX real-time operating system Those items can be harnessed to any autonomous vehicle for about $260 Since the programming and electronics are open source Reimer says it was easy to set the system up for his tractor The guidance system controls actuators that operate controls on his Deere 7930 tractor The tractor has a CVT gearbox that allows it to operate in the field and stop without changing gears or stalling The engine operates continuously at 1 500 rpm’s and uses an Outback hydraulic control valve for steering When he was putting the system together he learned that it was necessary to use a wheel angle sensor to soften the Pixhawk’s guidance signals so the tractor turns would be more gradual He took online training to develop programming skills so he could write about 600 lines of code to operate the system Aside from a small oil leak and a few stops for overheating the system operated flawlessly during the 2015 harvest Reimer says the system has fail safe steps built in to keep the tractor within view whenever they call it to the combine or in the field The 3D robotics digital radio that controls the tractor and the Pixhawk have a range of just over a mile The tractor will stop if it’s out of radio range Drivers filling their trucks from the grain cart use wireless key fobs to interrupt the signal from the controller so it doesn’t move unexpectedly as they’re unloading Reimer says he has replaced the labor of one person who’d normally operate the grain cart full time and put it to work in other parts of their farming operation In the winter of 2015-2016 he hopes to experiment with another system that might let him operate a second driverless seeding unit in the same field where he’s operating his planter He thinks a self-steering tractor could also be used for harrowing and rolling crops that now require a person to drive the tractor Contact: FARM SHOW Followup Matt Reimer 4-1-17 N E Killarney Manitoba R0K 1G0 Canada ph 204 523-8437