Combine Turned Into Handy Self-Propelled Auger
Charles Johnson along with his father and brother were tired of the time-consuming, backbreaking job of moving heavy grain augers at harvest time. They borrowed a few ideas from FARM SHOW readers and gathered up parts they had around the farm to build a self-propelled auger.
“All the engine and auger controls are reachable standing on the ground,” explains the Malta, Mont., farmer and rancher. “There’s no need to climb up onto the tractor to start and stop a pto-driven auger. And there’s no exposed pto shaft to work around near the intake end of auger.”
Besides being safer, it’s easier to operate.
“You can look straight up to the top end when positioning the auger at each bin. Also, the machine is not tippy when moving from bin to bin, and it’s not likely to tip over in high winds,” Johnson says.
The extra weight and engine came from a stripped down Model F Gleaner combine they bought at a neighbor’s auction. Johnson removed the cab and operator’s platform and lowered the engine frame as well as the radiator, hydraulic tank and pump to the bottom frame where the cleaning shoe had been.
He welded 5-in. sq. tubing to the main frame above and behind the rear axle to attach the original operator’s platform, and a combine header platform lift cylinder to raise the lower intake end of his 60-ft., 8-in. Speed King auger. He mounted a 60-in. hydraulic cylinder from a Farmhand F-10 loader under the grain auger tube to raise the auger, eliminating the need for the auger’s original cable winch.
The auger is driven by double groove pulleys from the combine, and its separator clutch stops and starts the auger. The cleaning fan shaft and pulley with an additional new pulley provide the right rpm speed for the jackshaft.
“We had to buy a heavier gearbox to get adequate belt pulley overhang strength as compared to the original pto gearbox,” Johnson says.
He built a transfer auger from the combine’s grain tank and unloading auger parts and a 240-volt electric motor power head from a bin floor sweep. He made mounting hardware so it attaches and detaches easily. That lets him use the power head for both jobs.
Johnson purchased a 12-volt gear reduction motor to power traction wheels (from a Toro riding lawn mower) under the transfer auger, which is operated by a toggle switch and heavy-duty relay mounted next to the operator’s platform.
“We have about $1,200 invested in the machine,” Johnson says. “We do a lot of shop projects, but this did have some challenges. We were surprised by the strength required in the auger A-frame to provide engine clearance. I would also consider doing a complete hydraulic motor drive instead of V-belt drive, and either an electric winch or hydraulic drive winch to raise and lower the auger. But these were the parts we had on hand, and the machine works very well.”
Contact: FARM SHOW Followup, Charles Johnson, 5861 Johnson Rd., Malta, Mont. 59538 (ph 406 658-2123; jwanddcj@itstriangle.com).
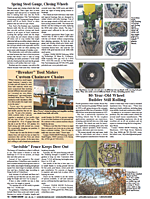
Click here to download page story appeared in.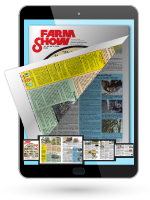
Click here to read entire issue
Combine Turned Into Handy Self-Propelled Auger AUGERS Charles Johnson along with his father and brother were tired of the time-consuming backbreaking job of moving heavy grain augers at harvest time They borrowed a few ideas from FARM SHOW readers and gathered up parts they had around the farm to build a self-propelled auger “All the engine and auger controls are reachable standing on the ground ” explains the Malta Mont farmer and rancher “There’s no need to climb up onto the tractor to start and stop a pto-driven auger And there’s no exposed pto shaft to work around near the intake end of auger ” Besides being safer it’s easier to operate “You can look straight up to the top end when positioning the auger at each bin Also the machine is not tippy when moving from bin to bin and it’s not likely to tip over in high winds ” Johnson says The extra weight and engine came from a stripped down Model F Gleaner combine they bought at a neighbor’s auction Johnson removed the cab and operator’s platform and lowered the engine frame as well as the radiator hydraulic tank and pump to the bottom frame where the cleaning shoe had been He welded 5-in sq tubing to the main frame above and behind the rear axle to attach the original operator’s platform and a combine header platform lift cylinder to raise the lower intake end of his 60-ft 8-in Speed King auger He mounted a 60-in hydraulic cylinder from a Farmhand F-10 loader under the grain auger tube to raise the auger eliminating the need for the auger’s original cable winch The auger is driven by double groove pulleys from the combine and its separator clutch stops and starts the auger The cleaning fan shaft and pulley with an additional new pulley provide the right rpm speed for the jackshaft “We had to buy a heavier gearbox to get adequate belt pulley overhang strength as compared to the original pto gearbox ” Johnson says He built a transfer auger from the combine’s grain tank and unloading auger parts and a 240-volt electric motor power head from a bin floor sweep He made mounting hardware so it attaches and detaches easily That lets him use the power head for both jobs Johnson purchased a 12-volt gear reduction motor to power traction wheels from a Toro riding lawn mower under the transfer auger which is operated by a toggle switch and heavy-duty relay mounted next to the operator’s platform “We have about $1 200 invested in the machine ” Johnson says “We do a lot of shop projects but this did have some challenges We were surprised by the strength required in the auger A-frame to provide engine clearance I would also consider doing a complete hydraulic motor drive instead of V-belt drive and either an electric winch or hydraulic drive winch to raise and lower the auger But these were the parts we had on hand and the machine works very well ” Contact: FARM SHOW Followup Charles Johnson 5861 Johnson Rd Malta Mont 59538 ph 406 658-2123; jwanddcj@itstriangle com