2016 - Volume #40, Issue #1, Page #27
[ Sample Stories From This Issue | List of All Stories In This Issue | Print this story
| Read this issue]
Process Turns Manure Into Liquid Gold
Alberta Agriculture researchers are turning manure into high-quality plant food with an aerobic bioreactor. Successful in the laboratory, the researchers’ next step will be setting it up at a poultry farm with the end product being used in a greenhouse or nursery. The process first turns manure into a slurry and then in 3 weeks turns it into mineralized, organic plant food.“It is a nutrient recycling, recovery system for livestock manure that makes utilization by plants near 100 percent,” says Nick Savidov, senior research scientist, Bio-Industrial Opportunities Branch, Alberta Agriculture and Rural Redevelopment. “We’ve been running trials for 3 years on high-value crops inside and outdoors, including one year in a greenhouse with tomatoes, and results are comparable or better than commercial fertilizer.”
Called “digestate”, the liquid fertilizer doubled the height of lodgepole pine and white spruce in 2 months. Seedling root mass was enhanced as was health, with improved resistance to root pathogens and greater nutrient uptake. Greenhouse tomatoes produced 15 percent higher yields with digestate than with commercial, synthetic fertilizers.
Savidov says the size-neutral system could be scaled up or down to match the manure output. It could also be used for human waste. Field crops will be the next step in research.
Manure is fed into a container with bacteria and a built-in agitator. Oxygen and water are added to create a slurry. The continually agitated mix ferments in an odor-free process for approximately 3 weeks. Once remaining solids have been filtered out, the digestate is ready to use.
Benefits include removing or reducing microbial problems like E. coli and salmonella that are present in manure. “During the process, E. coli drops an order of 10,000 times,” says Savidov. “It can’t survive the oxygenated fermentation process.”
Heavy metals can be problems in solid composting where 10 tons is concentrated into 1 or 2. With the liquid process, volume remains the same, keeping heavy metals at the same diluted levels as in the manure. Savidov says heavy metals could be precipitated out of the solution if necessary.
“The fermentation process also speeds up breakdown of antibiotics and other pharmaceuticals. “Our process speeds up what happens in nature,” he adds. “Things that take years in nature or months in dry composting happen in 2 weeks in our process.”
Savidov estimates the process could be ready to commercialize in 2 to 3 years. He says the system is built on aquaculture research done at the Crop Diversification Centre South, Brooks, Alberta.
“We separated solid waste from fish water and used aerobic reactors to solubilize it,” he says. “It was the first system that didn’t produce any waste at all, either in the aquaponic or food system. This project expanded that work to other livestock industries.”
Contact: FARM SHOW Followup, Food and Bio Processing Division, Agriculture and Forestry, Building F-83, 6020 – 118 Street; Edmonton, Alta. Canada T6G 2E1 (ph 780 644–8126; www1.agric.gov.ab.ca/$Department/deptdocs.nsf/all/bt14878).
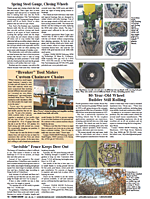
Click here to download page story appeared in.
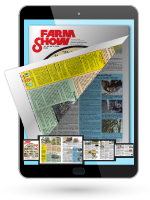
Click here to read entire issue
To read the rest of this story, download this issue below or click here to register with your account number.