2013 - Volume #37, Issue #1, Page #02
[ Sample Stories From This Issue | List of All Stories In This Issue | Print this story
| Read this issue]
Log Splitter Made From Scrapped Combine
![]() |
Bohlen’s project started when he found a junked Massey combine that had a decent drive train and frame. First he removed the feeder house and all of the harvesting components, leaving a bare frame with the original drive wheels, drive train and rear wheels. Since the combine’s original engine was hurting he replaced it with a Chrysler industrial flathead six. He also put in a new radiator, a 12-volt electrical system and a different gas tank. He mounted a 24 gpm hydraulic pump on the front of engine that powers the splitter and the auxiliary lift that he uses to raise heavy logs onto the splitter.
Bohlen says after getting the basic idea for the machine, he just figured it out as he went along. “There was very little frame left with most of the components of the combine gone so a 9-ft. long, 8-in. wide H-beam was added from the engine to the two rear wheels and that same beam became the main structure for the splitter mechanism.”
Wide flange beams are much easier to work with for log splitters than regular I-beams, notes Bohlen. A 4 by 30-in. long hydraulic cylinder moves the wedge to push the wood into the stationary pedestal. Pushing the wedge into the wood is much more convenient because you aren’t always dragging the pieces back that still need to be split again.
Bohlen says the combine’s hydraulic system provides plenty of power to split maple, oak and various hardwood logs. One side of the machine has a hydraulic hoist to lift heavy pieces of wood onto the splitter… “a real back saver,” Bohlen says.
The self-propelled splitter also has a hydraulic blade that’s mounted on fabricated arms on the front. The blade is useful for light duty work but the machine is too light in weight to push very much.
Much of the welding and fabrication done was a project for a student in a world-class vocational welding class in Burlington High School in Burlington, Iowa. The student did a great job and won a first place national award from the Lincoln Welding Company annual contest.
Contact: FARM SHOW Followup, Henry Bohlen, Wildlife Lakes Elk Farm, 13852 Washington Rd., West Burlington, Iowa 52655 (ph 319 752-4659; henry@wildlifelakes.com).
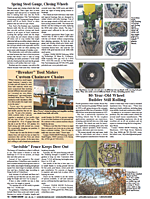
Click here to download page story appeared in.
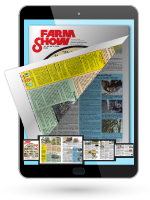
Click here to read entire issue
To read the rest of this story, download this issue below or click here to register with your account number.