Tractor Cab Memories
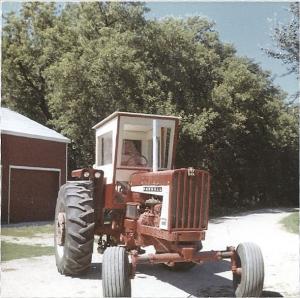 ✖  |
The story in our last issue about a farmer who built a wooden tractor cab brought back memories for contributing editor Lorn Manthey, who grew up on a farm in Southern Minnesota. “I made a tractor cab out of plywood 45 years ago in high school for my senior farm mechanics class. My dad agreed to let me install it on his new Farmall 706 tractor. My instructor and fellow students were skeptical that I could get it done.
“I drew up 3D plans in drafting class. My dad and I bought all of the materials for less than $50, including the steel, plexiglass windows, hinges, hardware and plywood. Dad’s only stipulation as he dropped the stuff off at school was to ‘make sure the darn thing’s done in time for spring field work.’
“The base supports were made from 1-1/2 in. box tubing. I U-bolted each side to the tractor axles on top of a 1/2-in. thick piece of belting to reduce noise and vibration. I made the cab frame from 2-in. angle iron that I welded on the corners with lap joints for extra strength. I built the frame on the shop floor and tipped it onto the tractor because my dad had said ‘be sure we can get the thing off without wrecking the tractor if I don’t like it.’ In all the years he owned it that never happened.
“With the frame completed, I cut 3/4-in. plywood for the roof/ceiling and 1/2-in. plywood for the walls, sides and door. I bolted the wood to the frame, then painted the exterior IH red and white to match the tractor. Inside I added foam panels to the sides and roof, then cut a large rubber mat for the floor and back that angled up and over the hydraulic lift arms. The windows were made of 1/4-in. plexiglass and mounted on aluminum tracks that I had cut from old combination storm windows. A sliding door and an AM/FM radio bolted to the ceiling rounded out the project, for which I received a nice red “A” for the semester. It might have been A+ had I not sounded the dual air horns a few too many times, disrupting a nearby study hall.
“That summer, after my dad had bragged to just about everyone he knew that ‘the kid had finally built something really useful’, a neighbor brought his new 806 diesel over and asked for the same cab. I built that one in about half the time and charged him a whopping $1.20 an hour for 40 hours of labor. My dad and his friend used their cabs for 6 to 7 years and I was never called on for warranty work.” Lorn Manthey, Contributing Editor
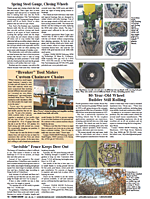
Click here to download page story appeared in.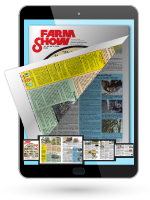
Click here to read entire issue
Tractor Cab Memories TRACTORS Cabs The story in our last issue about a farmer who built a wooden tractor cab brought back memories for contributing editor Lorn Manthey who grew up on a farm in Southern Minnesota “I made a tractor cab out of plywood 45 years ago in high school for my senior farm mechanics class My dad agreed to let me install it on his new Farmall 706 tractor My instructor and fellow students were skeptical that I could get it done “I drew up 3D plans in drafting class My dad and I bought all of the materials for less than $50 including the steel plexiglass windows hinges hardware and plywood Dad’s only stipulation as he dropped the stuff off at school was to ‘make sure the darn thing’s done in time for spring field work ’ “The base supports were made from 1-1/2 in box tubing I U-bolted each side to the tractor axles on top of a 1/2-in thick piece of belting to reduce noise and vibration I made the cab frame from 2-in angle iron that I welded on the corners with lap joints for extra strength I built the frame on the shop floor and tipped it onto the tractor because my dad had said ‘be sure we can get the thing off without wrecking the tractor if I don’t like it ’ In all the years he owned it that never happened “With the frame completed I cut 3/4-in plywood for the roof/ceiling and 1/2-in plywood for the walls sides and door I bolted the wood to the frame then painted the exterior IH red and white to match the tractor Inside I added foam panels to the sides and roof then cut a large rubber mat for the floor and back that angled up and over the hydraulic lift arms The windows were made of 1/4-in plexiglass and mounted on aluminum tracks that I had cut from old combination storm windows A sliding door and an AM/FM radio bolted to the ceiling rounded out the project for which I received a nice red “A” for the semester It might have been A+ had I not sounded the dual air horns a few too many times disrupting a nearby study hall “That summer after my dad had bragged to just about everyone he knew that ‘the kid had finally built something really useful’ a neighbor brought his new 806 diesel over and asked for the same cab I built that one in about half the time and charged him a whopping $1 20 an hour for 40 hours of labor My dad and his friend used their cabs for 6 to 7 years and I was never called on for warranty work ” Lorn Manthey Contributing Editor
To read the rest of this story, download this issue below or click
here to register with your account number.