2012 - Volume #36, Issue #1, Page #11
[ Sample Stories From This Issue | List of All Stories In This Issue | Print this story
| Read this issue]
Self-Taught Biodiesel "Expert"
![]() |
“I learned how to build this equipment the hard way, getting information from the internet, finding out it wasn’t always right, then spending two years perfecting the equipment and the process,” says Carrier. That trial and error process included learning from people who had started fires in their shop, burned down a garage and blown up a house. “There are a lot of things you can’t do, and some things you definitely shouldn’t do,” Carrier adds. “Don’t try to make the fuel under pressure in an old water heater, always use the correct amount of chemicals, protect the electrical hook ups with circuit breakers or fuses, and build your processor outside.”
To build his own processors, Carrier used parts from water heaters, relay switches from an air conditioner, small pumps from Harbor Freight, used bulk liquid containers, and new pvc and steel piping.
He first built a 40-gal. system that he says cost him less than $200. Now he has a 400-gal. processor with larger tanks, more elaborate piping and valves, better pumps and larger storage. He has about $4,000 into the larger system and produces very high quality biodiesel for less than $.80 a gallon. Both systems are free standing with excellent ventilation. They’re non-pressurized and the liquid never gets hotter than 130 degrees. Chemicals and methanol are added only after the heater is turned off.
Carrier uses waste cooking oil from restaurants as the base product for his biodiesel. Making fuel from waste oil gives him a product that has 30% lower emissions than low sulfur diesel from a pump. “Waste oil is available from many places,” Carrier says, “but a lot of restaurants have disposal contracts so you really have to work hard to find a regular source. My advice to anyone wanting to do this is to build the processor first, then find the oil source.”
Experience taught Carrier that waste oil stored in 35-lb containers will deteriorate over time. “I’ve heard of guys having plastic bottles fall apart and there’s oil everywhere,” he says with a laugh.
Carrier also learned that every batch of waste oil is different because of the temperature it was cooking at, the food it was cooking, how long it was stored after cooking, and what it was mixed with in storage. “We made a lot of weed killer with those early batches of biodiesel because we didn’t accurately test the oil for pH, free fatty acids and water before we started,” Carrier says. “Knowing those elements determines the amount of chemicals you need, and that’s very important.” He filters oil through an aluminum window screen to remove large particles before processing.
Carrier says the quality of his finished fuel is better than that he can buy at a station. “The industry standard for soap content is 66 ppm, and we can easily get to 30 ppm. Ours also has lower water content than industry standards allow, so we’ve got a product that’s better for the engines.”
Carrier runs his fuel in tractors and heavy equipment in a sand pit operation and says the engines are doing well. “We spend a lot of time getting the fuel processed right and making sure the quality is there because if we didn’t, we could ruin the injectors,” Carrier says.
One of the sources he recommends for competent information and quality components for making your own system is Utah Biodiesel Supply (http://utahbiodieselsupply.com). An internet forum for good information is 1earth@yahoo.com. Carrier says he’s also willing to advise biodiesel makers.
Contact: FARM SHOW Followup, Richard Carrier, 15840 Wimauma Rd., Wimauma, Fla. 33598 (ph 813 545-9361; harveyking@hotmail.com).
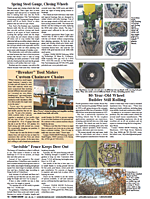
Click here to download page story appeared in.
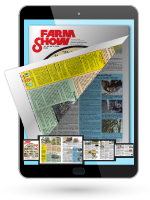
Click here to read entire issue
To read the rest of this story, download this issue below or click here to register with your account number.