2011 - Volume #35, Issue #6, Page #04
[ Sample Stories From This Issue | List of All Stories In This Issue | Print this story
| Read this issue]
Grain Bin Converted To Home For $9,000
![]() |
![]() |
![]() |
![]() |
The old farmhouse on the 1,280-acre place was too far gone to save. A peculiar idea kept coming back to the handyman who had built a few houses on his own over the years.
“One day, I was looking at the grain bins, and thought, ‘Maybe I can do something there’,” Thiebes recalled. He started playing around with the idea of building living quarters inside an unused 18-ft. dia., 2,800-bushel Columbia grain bin. “I was sitting here drawing pictures and I realized there was no reason I couldn’t do it.”
Four of the corrugated metal grain bins, probably from the 1960’s, are placed in a row on the property, which hasn’t been a working farm for some time. Of the four empty bins, Thiebes focused in on one of the end bins that already had a concrete floor and had a 15-ft. sidewall that would allow him to add a sleeping loft above a living area.
“How to fit square construction materials into a round structure took a little bit of thinking,” Thiebes said. “I would go to the Home Depot and sit there and look at things in every department to figure out what I could use.”
In April 2009, he started the project by mixing and floating several bags of leveling cement to fill cracks in the concrete floor. Next step was building the inner structure of the circular cabin.
By doing some calculations, he figured he could build 2 by 8-ft. boxes out of 2 by 4’s and create almost a perfect circle of studs around the 56-ft. circumference of the bin. After building the boxes and fastening them together inside the bin, he built another set of boxes, only 7 ft. high, to create the walls for the second story, and then tied the upper and lower stud walls together.
Thiebes then moved outside, drilling 3 holes in the bin to attach each stud through the metal wall. He used 2 ˝-in. roofing screws with rubber gaskets to fasten each stud from the outside.
The combined structure of the metal building and the wood interior studs made for a strong building, but Thiebes had a question that nobody, including the grain bin manufacturer, could answer: What would happen to the structural integrity of the bin when he cut several window openings? As it turned out, he cut several 2-ft. sq. openings and noticed no difference.
Thiebes fitted the holes with 2 by 2-ft. vinyl slider windows because that was the smallest standard size available, and they fit perfectly between his wall studs. He installed one bigger picture window – in the kitchen, overlooking 700 acres of wheat fields – because a lumberyard gave him the window for free. Another hole was cut for a 10,000 btu window air conditioner.
The floors were next. Thiebes laid two vapor barriers on the concrete floor, 6-mil plastic first, then 90-lb. roofing felt. To that he added a floating subfloor made for basement applications, consisting of 7/16-in. OSB panels with a plastic waffle backer to act as another vapor barrier. Oak laminate flooring was used to finish both levels.
For the loft, Thiebes fixed 2 by 10-in. floor joists, 2 ft. on center, supported around the first floor ceiling by triple 2 by 4’s nailed together to make posts. One-third of the second floor was left open to view the bin ceiling. Tongue-and-groove flooring was screwed and glued into place and topped by the laminate.
Walls were insulated with green R-13 fiberglass batting; the metal bin ceiling was left exposed. Metal L flashing for roofs was used to trim the windows. Interior walls were finished with drywall, the seams covered by 1 by 4-in. wood strips. Flexible interior trim and garage door weather-stripping was used to cover gaps where the flooring and round wall didn’t fit perfectly. The interior was painted with textured paint.
A standard metal exterior door with a window that opens was installed just inside the bin’s manway, which remains as a security door that’s padlocked between visits.
Half of the first floor is a living room with a couch, chairs and a square 2 by 2-ft. wood stove that keeps the house warm in the winter (two portable oil-filled radiator heaters provide heat when the stove isn’t lit). The other half of the main floor is split between a kitchen and a bath with shower. The kitchen has hickory cabinets, an electric cooktop, a microwave oven and an under-counter refrigerator.
The bath features an “Incinolet” electric incinerating toilet that turns waste into ash, saved Thiebes the expense of installing a septic system (www.incinolet.com). Graywater from the bath and kitchen are drained out onto the grass.
To reach the loft, Thiebes built a wooden ladder. The loft includes dual bunk beds. Overhead there’s a ceiling fan painted to match the color of the bin ceiling. Thiebes said it’s almost invisible.
To keep plumbing cost and maintenance down, Thiebes installed flexible polyethylene tubing instead of copper and he didn’t need any conventional traps, which makes the house simple to close up for winter. To make sure the building would be safe from a lightning strike, Thiebes incorporated two grounding rods and ran a separate copper grounding wire through the bin.
The bin is used throughout the year, especially during hunting season and holidays, mostly by Thiebes and his sons. One son wants to move to the farm after college, and they are toying with the idea of using the other three bins, set up in a triangle and joined by passageways, to create more lodging.
Completed in September 2009, Thiebes said the grain bin house is sturdy, cozy and cost-effective. The entire project cost about $9,000 to complete, and $1,000 of that was for the high-tech toilet. He thinks abandoned grain bins could be converted into useful housing for many in farm country.
Contact: John Thiebes, 225 Arbour Dr. E, Kalispell, Mont. 59901 (ph 406 257-5788; kthiebes@hotmail.com).
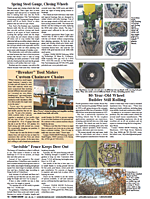
Click here to download page story appeared in.
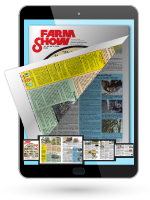
Click here to read entire issue
To read the rest of this story, download this issue below or click here to register with your account number.