2011 - Volume #35, Issue #3, Page #38
[ Sample Stories From This Issue | List of All Stories In This Issue | Print this story
| Read this issue]
He Turned An Alternator Into A Great Stick Welder
![]() |
"A normal automotive alternator can be used for a welder, but is limited to 60 to 70 amps output current," says Toppen. "If you're a welder, you know it's nice to have a higher output current than this. I used a truck alternator with double-drive belts and from 135 to 185 output amps. This makes for a nice capacity unit."
The used truck alternator is brushless with a stationary field coil that protrudes into the double V-belt driven field shell. This allows Toppen to put larger amounts of voltage into the field coil without overtaxing brushes. Otherwise, the alternator had the usual regulator, diode trio and bridge rectifier under the plate on the end cap.
"I removed the plate which let me also remove the regulator and the diode trio that I didn't need as I didn't want them regulating (limiting) output," explains Toppen. "I also removed the bridge rectifier and replaced it with an RD-05 from Regitar. It doesn't use avalanche diodes, which it's said don't last long in a welder."
With those minor changes, sandblasting and repainting parts, Toppen had his welder. With the help of a friend, he bent steel plate to make a mounting frame for the front of his Sears garden tractor. Its 12 hp Koehler engine had pulleys in place for various Sears add-ons that made it ideal to power the welder.
"I still needed to get the rpm's up from the tractor engine's 3,200 to 3,600 maximum rpm's to the 7,000 to 8,000 I needed for the alternator," says Toppen. "I added a jackshaft with a two-stage gear induction."
To allow for adjusting the belt drive, Toppen machined a lengthwise slot in the adapter plate. He used pieces of square tubing to raise the welder and to mount it to the plate for easy adjusting.
"I knew I would need 40 to 50 volts and around 80 amps to get a decent arc when welding," says Toppen. "My 12 hp engine was more than sufficient in power. The 50 amps times 80 volts equals 4,000 watts, which is equal to 5 hp. We got another 7 hp to work with."
A pair of low cost jumper cables connects the garden tractor battery to alligator clamps on the field to power up the coil. Welding cables connect to the output posts on the alternator.
The first time Toppen fired up the welder, he selected an all purpose rod and a heavier duty rod. He quickly found he could adjust the engine rpm's to the welding rod to find its particular output "sweet spot".
"The great thing is that I can use it on the garden tractor the way I have it, or I can mount it on a full size tractor or even under the hood of a pickup if there's room for a jackshaft," says Toppen. "I've done equipment repairs in the field, welding tongues back on wagons and such. It adds real versatility to the shop."
Toppen offers more in-depth instructions for making the portable welder on a CD that he sells for $15 plus $3 shipping. The CD, along with other Toppen instructional CD's, is available on Toppen's eBay store. It includes high quality images, schematics and wiring diagrams. Also included are modifications to use the portable welder as a TIG torch and for running a carbon arc torch. He also explains how the welder can be used to power brush-type motors.
Contact: FARM SHOW Followup, Mike Toppen, P.O. Box 138, Burnips, Mich. 49314 (ph 269 673-5597; fordsrule@btc-bci.com; http://site.toppentech.com/; http://stores.ebay.com/TOPPENTECH).
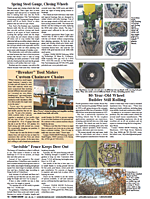
Click here to download page story appeared in.
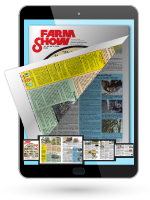
Click here to read entire issue
To read the rest of this story, download this issue below or click here to register with your account number.