Manure Drying System Fuels Itself
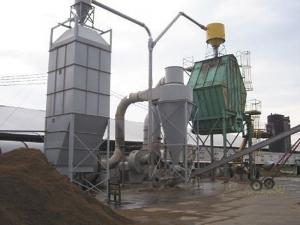 ✖  |
Faced with high costs for bedding and hauling manure, Van Der Geest Dairy solved both problems and more. The 3,000-cow operation installed a manure drying system that eliminates hauling 4,500 loads of solids to the fields. It also replaces five to six semi loads of sawdust with dried manure. Best of all, it fuels itself with dried manure.
"About 50 percent of the material ends up as fuel," says Lee Van Der Geest. "The neat thing is it doesn't just dry cow manure, but also waste feed, pen pack material, and green sawdust. Anything organic can be run through it. And we're bedding our stalls heavier than ever, and that lowers our somatic cell count."
The system consists of the dryer from Energy Unlimited, Inc. and a manure solids separation process. About 30 percent of manure solids are separated out of manure flushed from the milking parlor and freestyle barn. The solids are sent through a rotary drum dryer where they're heated to 1,000 degrees F, killing any bacteria and pathogens and making the product safe for use as bedding as well as fuel to fire the 1,500 degree furnace.
Water from the separation process is used to process and cool the exhaust from the furnace and dryer. After solids have been removed, it is pumped to a concrete trench where the exhaust heat is incorporated with paddles that oxygenate the liquid. Ammonia is eliminated by aerobic bacteria growth aided by the heat and the oxygen. The high temperature exhaust cools to about 100 degrees. Once the water has been "air scrubbed", it's reused to flush the barn and parlor floors, and the process repeats.
Even the ashes from the furnace have a use. "We clean out about two wheelbarrow loads of ash per day and set it aside to apply to our crop fields," says Van Der Geest. "It's extremely high in potassium."
Van Der Geest notes the last time he had checked prices, potassium was selling for $650/ton. That combines with eliminating most sawdust, which has increased in price with the popularity of wood pellet furnaces. Add in savings in fuel from reduced trips to the field with manure solids, and the system is paying for itself, he says.
While the Van Der Geest dairy was the first manure drying installation for Energy Unlimited, it isn't the last. The company has been building dryers for wood pellets, alfalfa and other products for 20 years. They're putting in more units at dairies and have also installed one in Georgia to dry tree shavings for use in poultry litter. The trees are thinned from loblolly and Southern pine plantations.
"Dry shavings were $100 per ton," says John Lindell, Energy Unlimited. "The thinned logs only cost them $25 per ton. With our biofeed furnace, they can replace natural gas, and payback is even faster."
Lindell admits the unit requires a minimal three-tons/hour size to be economical. He notes that Van Der Geest's unit handles four-ton/hour, and their dryer/furnace unit would be priced around $400,000.
Contact: FARM SHOW Followup, Energy Unlimited, Inc., P.O. Box 7, 4881 Highway YZ, Dodgeville, Wis. 53533 (ph 608 935-9119; fax 608 935-0008; info@ energy unlimitedinc .com; www. energy unlimited inc.com).
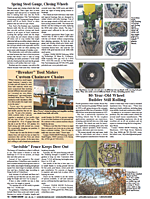
Click here to download page story appeared in.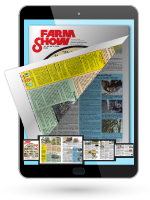
Click here to read entire issue
Manure Drying System Fuels Itself ENERGY Alternative Fuels 32-3-4 Faced with high costs for bedding and hauling manure, Van Der Geest Dairy solved both problems and more. The 3,000-cow operation installed a manure drying system that eliminates hauling 4,500 loads of solids to the fields. It also replaces five to six semi loads of sawdust with dried manure. Best of all, it fuels itself with dried manure.
"About 50 percent of the material ends up as fuel," says Lee Van Der Geest. "The neat thing is it doesn't just dry cow manure, but also waste feed, pen pack material, and green sawdust. Anything organic can be run through it. And we're bedding our stalls heavier than ever, and that lowers our somatic cell count."
The system consists of the dryer from Energy Unlimited, Inc. and a manure solids separation process. About 30 percent of manure solids are separated out of manure flushed from the milking parlor and freestyle barn. The solids are sent through a rotary drum dryer where they're heated to 1,000 degrees F, killing any bacteria and pathogens and making the product safe for use as bedding as well as fuel to fire the 1,500 degree furnace.
Water from the separation process is used to process and cool the exhaust from the furnace and dryer. After solids have been removed, it is pumped to a concrete trench where the exhaust heat is incorporated with paddles that oxygenate the liquid. Ammonia is eliminated by aerobic bacteria growth aided by the heat and the oxygen. The high temperature exhaust cools to about 100 degrees. Once the water has been "air scrubbed", it's reused to flush the barn and parlor floors, and the process repeats.
Even the ashes from the furnace have a use. "We clean out about two wheelbarrow loads of ash per day and set it aside to apply to our crop fields," says Van Der Geest. "It's extremely high in potassium."
Van Der Geest notes the last time he had checked prices, potassium was selling for $650/ton. That combines with eliminating most sawdust, which has increased in price with the popularity of wood pellet furnaces. Add in savings in fuel from reduced trips to the field with manure solids, and the system is paying for itself, he says.
While the Van Der Geest dairy was the first manure drying installation for Energy Unlimited, it isn't the last. The company has been building dryers for wood pellets, alfalfa and other products for 20 years. They're putting in more units at dairies and have also installed one in Georgia to dry tree shavings for use in poultry litter. The trees are thinned from loblolly and Southern pine plantations.
"Dry shavings were $100 per ton," says John Lindell, Energy Unlimited. "The thinned logs only cost them $25 per ton. With our biofeed furnace, they can replace natural gas, and payback is even faster."
Lindell admits the unit requires a minimal three-tons/hour size to be economical. He notes that Van Der Geest's unit handles four-ton/hour, and their dryer/furnace unit would be priced around $400,000.
Contact: FARM SHOW Followup, Energy Unlimited, Inc., P.O. Box 7, 4881 Highway YZ, Dodgeville, Wis. 53533 (ph 608 935-9119; fax 608 935-0008; info@ energy unlimitedinc .com; www. energy unlimited inc.com).
To read the rest of this story, download this issue below or click
here to register with your account number.