2003 - Volume #27, Issue #3, Page #38
[ Sample Stories From This Issue | List of All Stories In This Issue | Print this story
| Read this issue]
Portable Welding Shop Mounts On Old Garbage Truck
![]() |
Over the years, he's put together six different rigs to haul tools and power to welding sites. "I've put them on trailers and smaller trucks, but I never had one that would handle everything I might need. I was always running back to the shop for something," he says.
So for his newest portable welding rig, Esser found a 1981 C70 2-ton Chevrolet truck cab and chassis and went to work. "The truck had been a single axle garbage truck, so it already had a good set of springs under it," he says.
"The first thing I did was to extend the frame, making it 30 ft. long from bumper to bumper," he says.
Then he built a utility bed on it that's only a 20-in. step up between the wheels. "I made shelves and compartments all around it that are accessible from the ground, as is all," he says.
With the exception of one tool cabinet, he made all the cabinets on the truck from aluminum deckplating. All have hinged, locking doors.
Besides welding tools and supplies, his cabinets hold the equivalent of a small hardware store. "I have large quantities of the most common sizes of screws, bolts, nuts, steel rod, flat steel, angle iron, etc., on the truck," he says. "It's often a 20-mile round trip or more to the closest hardware store, so having the truck stocked saves a lot of time and expense. A trip to the hardware for four or five bolts costs the customer an hour of my time or more."
Most of the welding equipment and storage is centered around a 50-ton iron worker that he uses to cut and shape steel on site.
Then there's an 8,000-watt gasoline engine-powered generator, a 250-amp stick welder and a 250-amp wire feed welder. He mounted oxygen and acetylene tanks on one side, with 100 ft. of hose that lets him get his torch into just about any place where he needs it.
The generator provides power for the welders, and several other power shop tools, including a drill press. Tucked into one of the cabinets is 200 ft. of 220-volt power cord, so he can take the welders off the truck if he needs to.
Other components include portable and fixed lighting, so he can work any time of day or night. Some of his portable lighting draws power from the generator. For the truck mounted lights, though, he replaced the stock alternator with a heavy-duty 100 amp model, which keeps the truck battery and a bank of back up batteries well charged.
Tucked into one cabinet is a 220-volt air compressor with 150 ft. of hose. The compressor is plumbed into outlets on both sides of the truck, so he doesn't have to run the hose over or under the truck to get to his work. "I had another smaller compressor on the truck at first, but it didn't put out enough air for my plasma cutter," he says.
There wasn't room for the plasma cutter on the truck and Esser says he doesn't usually need it. When he does, he takes it along on a pallet that fits into the receiver hitch on back of the truck.
While he spent a lot of time designing the truck, he says he had to make some changes and it took quite a bit of on-the-spot engineering to get it all to fit together. One of the main concerns in the design was that the truck fit inside his shop, which has a 96-in. doorway.
He figures he has more than $50,000 invested in the portable welding shop, including his small rolling hardware store.
Contact: FARM SHOW Followup, Brian Esser, 53478 250th St., Minnesota Lake, Minn. 56068 (ph 507 462-3651; email: bndesser@bevcomm.com).
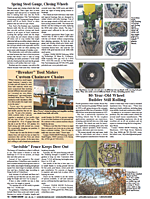
Click here to download page story appeared in.
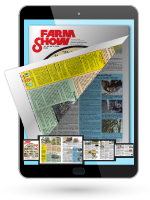
Click here to read entire issue
To read the rest of this story, download this issue below or click here to register with your account number.